Precision CNC Machining Services: Enhancing Manufacturing Accuracy
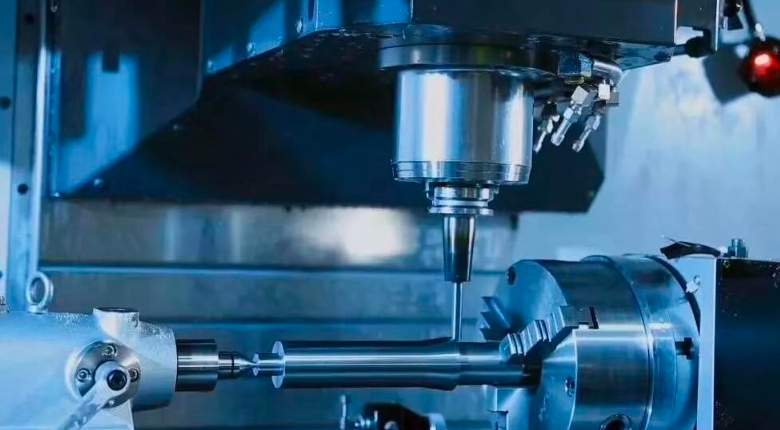
In the modern manufacturing industry, precision is a critical factor that determines the quality and performance of a product. Precision CNC machining services play a vital role in ensuring that components meet exact specifications with minimal deviations. Whether in aerospace, medical, automotive, or electronics industries, precision machining delivers high-quality parts with outstanding accuracy and reliability.
This article explores precision CNC machining services, their benefits, applications, and how they compare to traditional manufacturing techniques.
Understanding Precision CNC Machining Services
Precision CNC (Computer Numerical Control) machining refers to the process of manufacturing components with extremely tight tolerances using computer-controlled tools. These machines follow programmed instructions to cut, shape, and drill raw materials, ensuring consistency and repeatability.
The process starts with a CAD (Computer-Aided Design) model, which serves as a blueprint for the CNC machine. Using CAM (Computer-Aided Manufacturing) software, the design is translated into machine instructions, guiding the cutting tools to produce the desired part. This method minimizes human error and guarantees high precision, even for complex geometries.
Advantages of Precision CNC Machining Services
1. High Accuracy and Consistency
Precision CNC machining achieves tolerances as tight as ±0.001 inches, making it ideal for industries requiring exact specifications. Each part produced is identical, ensuring uniformity in large production runs.
2. Efficiency and Speed
CNC machines operate at high speeds, reducing production time. Once the program is set, the machine can run continuously with minimal supervision, increasing efficiency.
3. Versatility in Material Selection
Precision CNC machining works with various materials, including metals (aluminum, steel, titanium), plastics, composites, and ceramics. This allows manufacturers to choose the best material for their application.
4. Reduced Waste and Cost Savings
Since CNC machining is highly precise, it minimizes material wastage. This leads to cost savings, particularly in industries where raw materials are expensive.
5. Complex Geometries and Intricate Designs
Unlike traditional machining, CNC technology can create intricate parts with complex geometries, making it suitable for advanced engineering applications.
6. Automation and Reduced Labor Costs
CNC machining is largely automated, requiring fewer operators. This reduces labor costs and eliminates errors associated with manual machining.
Industries That Benefit from Precision CNC Machining Services
1. Aerospace Industry
Aircraft components demand extreme precision due to strict safety regulations. CNC machining is used to manufacture engine parts, turbine blades, and structural components with exact specifications.
2. Medical Sector
Medical devices such as surgical instruments, implants, and prosthetics require precise machining to meet stringent healthcare standards. CNC technology ensures these components function correctly and safely.
3. Automotive Manufacturing
Precision CNC machining plays a crucial role in producing engine components, transmission systems, and custom car parts. High tolerance levels ensure optimal vehicle performance and safety.
4. Electronics Industry
Small, intricate parts like circuit board housings, connectors, and heat sinks are produced using CNC machining, ensuring high precision and functionality.
5. Defense and Military Applications
CNC machining is used to manufacture weapons, surveillance equipment, and specialized military components that demand high accuracy and durability.
Precision CNC Machining vs. Traditional Machining
Feature | Precision CNC Machining | Traditional Machining |
Accuracy | ±0.001 inches or better | Lower accuracy due to manual operation |
Speed | High-speed automated process | Slower, requires manual adjustments |
Complexity | Can create intricate designs | Limited to simpler shapes |
Material Waste | Minimal waste due to precision | Higher waste due to manual errors |
Consistency | High repeatability | Variations may occur between parts |
Labor Cost | Lower due to automation | Higher due to manual labor |
While traditional machining is still used for some applications, precision CNC machining services offer significant advantages in speed, accuracy, and efficiency, making them the preferred choice for modern manufacturing.
Key Technologies in Precision CNC Machining
Precision CNC machining services utilize advanced technologies to enhance manufacturing capabilities. Some of these include:
1. Multi-Axis Machining
CNC machines come in 3-axis, 4-axis, and 5-axis configurations, allowing for complex cutting and shaping of materials from multiple angles without repositioning the workpiece.
2. Electrical Discharge Machining (EDM)
EDM is used for machining hard metals and creating intricate designs that traditional cutting tools cannot achieve. It works by eroding the material using electrical sparks.
3. Laser and Waterjet Cutting
These non-contact cutting methods ensure high precision while reducing heat-related distortions in delicate materials.
4. Advanced Tooling Systems
Modern CNC machines use high-speed cutting tools, carbide inserts, and automated tool changers to enhance efficiency and precision.
5. Real-Time Monitoring and Quality Control
With AI and IoT integration, CNC machining centers now offer real-time monitoring, ensuring process stability and immediate detection of any defects.
Steps in the Precision CNC Machining Process
The precision CNC machining process follows a structured approach to ensure the highest quality output.
1. Designing the Part
A CAD model is created, detailing dimensions, tolerances, and material specifications.
2. Programming the CNC Machine
The design is converted into G-code, a language that CNC machines use to execute precise movements.
3. Material Selection
Choosing the appropriate material based on strength, durability, and application requirements.
4. Machining the Component
The CNC machine performs cutting, drilling, milling, or turning operations according to the programmed instructions.
5. Finishing and Inspection
After machining, the part undergoes deburring, polishing, and surface treatments. Quality control checks ensure compliance with specifications.
Choosing the Right Precision CNC Machining Service Provider
Selecting the best CNC machining service provider is crucial for achieving high-quality results. Consider the following factors:
1. Experience and Reputation
A provider with years of experience in precision CNC machining services will have the expertise to handle complex projects.
2. Technological Capabilities
Ensure the company uses advanced multi-axis CNC machines, high-speed tooling, and real-time monitoring for precision manufacturing.
3. Material Expertise
Different industries require different materials. Choose a provider that offers expertise in working with metals, plastics, ceramics, and composites.
4. Quality Control Standards
Look for providers with ISO 9001, AS9100, or medical-grade certifications to ensure compliance with industry standards.
5. Customization and Flexibility
A good CNC machining service should be able to handle custom designs and low-volume prototypes as well as large-scale production.
6. Competitive Pricing and Lead Time
Compare pricing, turnaround times, and overall value to select the best provider for your needs.
Future Trends in Precision CNC Machining
The future of precision CNC machining services is shaped by technological advancements that improve efficiency and accuracy. Some emerging trends include:
1. AI and Machine Learning Integration
CNC machines are increasingly using AI algorithms to predict tool wear, optimize cutting paths, and reduce errors.
2. Robotics and Automation
Automated robotic arms are now integrated into CNC machining for faster material handling and reduced labor costs.
3. Sustainable Machining Practices
The industry is moving toward eco-friendly machining techniques, such as reducing coolant waste and using recyclable materials.
4. Hybrid Manufacturing
Combining CNC machining with additive manufacturing (3D printing) allows for faster prototyping and complex part production.
Conclusion
Precision CNC machining services are transforming the manufacturing landscape by offering unparalleled accuracy, efficiency, and material versatility. From aerospace and medical to automotive and electronics, industries rely on CNC machining to create high-precision components that meet strict specifications.
As technology continues to evolve, precision CNC machining will become even more advanced, integrating AI, automation, and sustainable practices to further enhance manufacturing capabilities. For businesses looking to achieve superior quality and consistency in their products, investing in precision CNC machining services is a strategic move toward success.